3次元測定機(CMM)ベースの検査工程を再現する
InnovMetric Softwareは、 3DデジタイザーとPolyWorks®を利用してCMMベースの検査工程を再現しました。
現在、自動車や航空宇宙産業のメーカーは、部品、鋳物、金型などの検査にタッチプローブ式のCMMテクノロジーを使っています。この検査工程は際立って正確で信頼が出来ると、長い時間をかけて判明されましたが、同時に、多大な時間を必要とする上に割高であるという事も判明されました。
3Dデジタイズテクノロジーの出現と発展は、近年自動車や航空宇宙産業界において沢山の新たな活用チャンスを提供しています。検査と品質管理分野における最新の画期的な革新、つまり3Dデジタイザーと高密度の点群検査ソフトウエアが、従来のゲージやCMMのような様々なツールを使って管理してきた一連の検査を再現します。
InnovMetric Software は2000年以降、高密度点群を使い、鋳物/金型/鋳型の品質を管理し、プロトタイプ/初回製品/製造・組立て部品検査工程を通して生産工程を承認する、強力なソフトウエアソリューションであるPolyWorks|Inspector™を提供しています。PolyWorks|Inspector™ は形状を比較する(部品と部品や、部品とCAD)為の完全なツールセットであり、多様な測定ツール(直線、半径、段差隙 、厚さ等)はもちろん、完全な幾何寸法公差 解析機能も含んでいます。
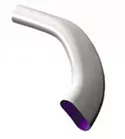
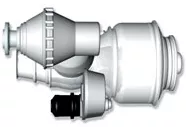
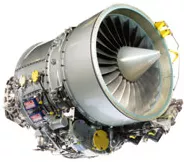
課題
InnovMetric は、世界トップレベルのジェットエンジンメーカーであるPratt & Whitney Canada に、従来の3次元測定機の代わりにPolyWorksと3D デジタイザーを使い、伝統的な部品検査を再現するように依頼されました。そこでまず、InnovMetricのアプリケーションエンジニアは Pratt & Whitney Canadaの開発チームと共に、PolyWorksで取得された結果の品質を評価する為、ディフューザーパイプの標準的な検査を実施し、それらを3次元測定機で取得した結果と比較しました。このテストから、PolyWorksは今までのプローブベースの測定工程にかかる時間に比べて、僅かな時間で正確な結果を提供出来る事が証明されました。
解決策
このテストでは、ディフューザーパイプ(ジェットエンジン内部にある、圧縮空気を圧縮システムから燃焼室に運ぶ部品)を使い、 PolyWorks|Inspector™ ソフトウエアソリューションでの標準的な検査が実施されました。 「PolyWorks は現物の部品上でプローブ検査をする代わりに、測定された点群データ上でプローブ検査をするバーチャルCMMの様に作動します。この機能によって、品質管理スペシャリストは何万もの点を集める事が出来、より豊富でより完全な情報源を元に解析する事が可能になります。」とInnovMetric Software Inc.の代表取締役社長であるMarc Soucy氏は述べています。
テストは、以下の5つの手順で実施されました:
A) データ収集:
手順 1. データを取得する
ディフューザーパイプは3Dデジタイザーでデジタイズされます。高密度の点群が取得され、豊富な情報源が品質管理スペシャリストへ提供されます。
B) PolyWorksで点群を処理する:
手順 2. 最初の位置合わせと全体的な比較
- デジタイザーから取得された点群はグローバルベストフィット位置合わせ方法を用い、CADモデルに位置合わせされます。
- 点群とCADモデルが比較される事により点-CAD偏差が取得され、OK/NGレポートが生成されます。
手順 3. 2回目の位置合わせ
CMM位置合わせを再現する為、3つの断面から引き出された特定のフィーチャー(平面、ベクトル、 原点)を使い、 3-2-1 位置合わせを実行します。
手順 4. 測定と比較
GD&T プログラミング技術と断面解析が使われ、16断面における4つの測定結果が取得されます:
- 面積測定 (断面から)
- ボウの変位量 (GD&T)
- N 角度 (GD&T)
- 最大偏差 (断面から)
手順 5. レポート生成
カラーマップ、集計表、注釈付きのスナップショットを含む、完全なレポートが作成されます。レポートはその後、ASCII、AVI、 Excel、 HTML、 VRML、 Wordを含む各ファイルフォーマットにエクスポートされます。
PolyWorks|Inspector™ は従来のCMMの精度を保持しながら、ディフューザーパイプの検査時間を75%以上削減しました。
メリット
このテストにおけるPolyWorksの特に目立った特性は以下になります。
- 断面解析
デジタイズ点とCADサーフェス間のグルーバル比較は、製造過程で発生した複雑な変形を可視化する手助けをしてくれる強力なツールです。しかし大抵の場合、部品の機能は通常明確な寸法リストによって決まる為、グローバルカラーマップだけでは部品の合格/不合格判定 には不十分です。ディフューザーパイプの場合、パイプセンターラインに沿った断面積の段階的な変化が、その部品が仕様に合うかどうかを決定する最も重大な特性になり、もしグローバル点-CAD偏差だけが検査工程においての唯一の検討基準であったとしたら、仕様に合った多くのディフューザーパイプが無駄に却下される事もあり得ます。
- 幾何寸法公差(GD&T)解析
PolyWorks|Inspector™独自の特徴として、それぞれにユーザー定義の許容値を持つ事が可能な各プログラム測定がある、フィーチャーベース測定工程があります。このプロジェクトにおいて、PolyWorks|Inspector™の幾何公差ツールは、基準CADフィーチャー間の関係、必要とされる測定、及び各測定に対する特定の許容値を定義するのに使われます。幾何公差オブジェクトが自動的に点群上の実寸法を計算し、許容値に沿ったOK/NGレポートを作成します。
-
強力なマクロプログラミング言語
CMMで取得したデータを解析するには、大抵 とても時間がかかります。様々な測定結果を取得する為にデータは様々なソフトウエアにロードされ、そしてその他の工程は手動で実行されなければなりません。また全ての新しい部品に対して、各工程を繰り返し行う必要があります。
PolyWorksであれば、一連の測定が高度なマクロプログラミング言語を利用して自動的に行われます。ある試みでは、一人のInnovMetric 社のアプリケーションエンジニアが2日とかからずに、全検査工程をオートメーション化するマクロを開発し、その結果エンジニア達は最初の位置合わせから完全なレポートの作成までの全点群検査を、マウスを1クリックするだけで3分とかからずに実行する事が出来る様になりました。
結果
10%ルールに基づくと、スキャン結果とCMM結果間の違いが部品許容値の10%より低いので、 予備段階での結果は許容範囲内でした。これらの結果をさらに立証する為のR & R (繰り返し性と再現性)ゲージ テストも、今は実行可能となりました。
要旨
テストの目的
-
点群データを取り込むのに3Dデジタイザーを利用し、データを処理するのにPolyWorksを利用して、従来のCMMベース検査工程を再現する。
-
PolyWorks で取得した測定結果の品質(精度)を、CMMで取得したものと比較して評価する。
-
PolyWorksを使い、部品の検査を完了するのにかかる時間を評価する。
-
R & R (繰り返し性と再現性)ゲージ テストの成功の可能性を立証する。
取り組み
-
高密度レーザーベースデジタイザーでディフューザーパイプをデジタイズする。
-
データ点群をPolyWorksにインポートし、IMInspectモジュールを使って、オリジナルのCADモデルに位置合わせする。
-
PolyWorksで事前にプログラムされた幾何寸法公差解析ツールと断面解析機能を使い、自動的に16断面における4つの測定結果を引き出す。
-
カラーマップ、注釈付きスナップショット、表形式のレポート、AVI形式での動画レポートを含む完全なレポートを作成する。
-
PolyWorksのスクリプト言語を使ってマクロを開発し、全検査工程を自動化する。
テスト結果
-
3D デジタイザーとPolyWorksで得られる測定結果はCMMで得られる結果に非常に近い。この2組の結果間の偏差は部品許容値の10%未満である。
-
3DデジタイザーとPolyWorksを使ったディフューザーパイプの検査時間は、従来のCMMベース検査技術と比較すると25%未満:
• 3Dデジタイザーでのデータ取得 には、CMMでは1時間かかるのに対し、15分しかかからない。
• PolyWorksの完全 に自動化された検査機能を使うと、点群検査工程が3分とかからずに完了する。