より高い効率性を目指して
PolyWorks®、油田装置メーカーにおけるモーター部品の検査時間の50%短縮に貢献
Weatherford International Ltd.は、精力的に営業を続けている世界有数の油田サービス企業です。米国テキサス州ヒューストンに本社を置き、全世界に3万4千人以上の従業員を擁して100カ国以上710カ所以上の拠点で事業を展開しています。同社のカナダ、アルバータ州エドモントンにある施設では、油井採掘後の石油生産で使用される一軸ねじポンプと油圧セクションの2つの石油生産用製品を設計および製造しています。
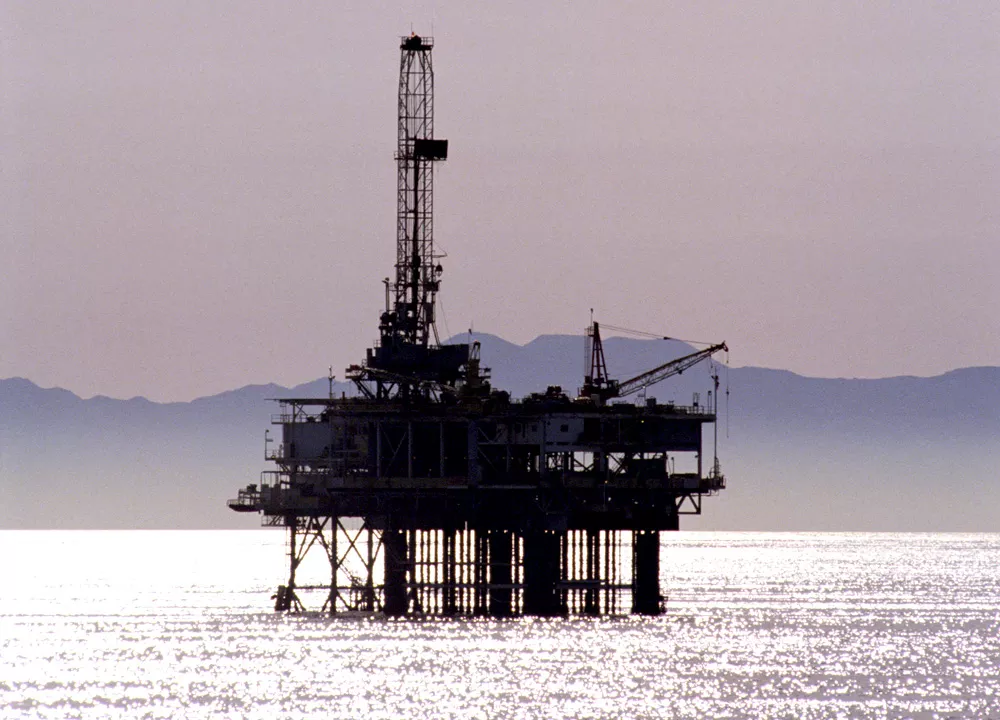
課題
世界の石油・ガス採掘業界において急増する需要を満たすため、Weatherford社は生産を強化してきましたが、それとともに検査作業の効率向上の必要性も強くなっていました。
Weatherford社の製品は、世界中の大手石油生産企業の生産操業をサポートしており、同社のカナダ、アルバータ州エドモントンにある施設では、油井採掘後の石油生産で使用される一軸ねじポンプと油圧セクション (油井を採掘するための動力を供給するモーター) の2つの石油生産操業用製品を設計および製造しています。同社では生産効率を引き上げるため、非常に複雑な形状を持ち、従来の方法では検査が難しい油圧セクションをより効率的に検査するために新しい検査方法を求めていました。
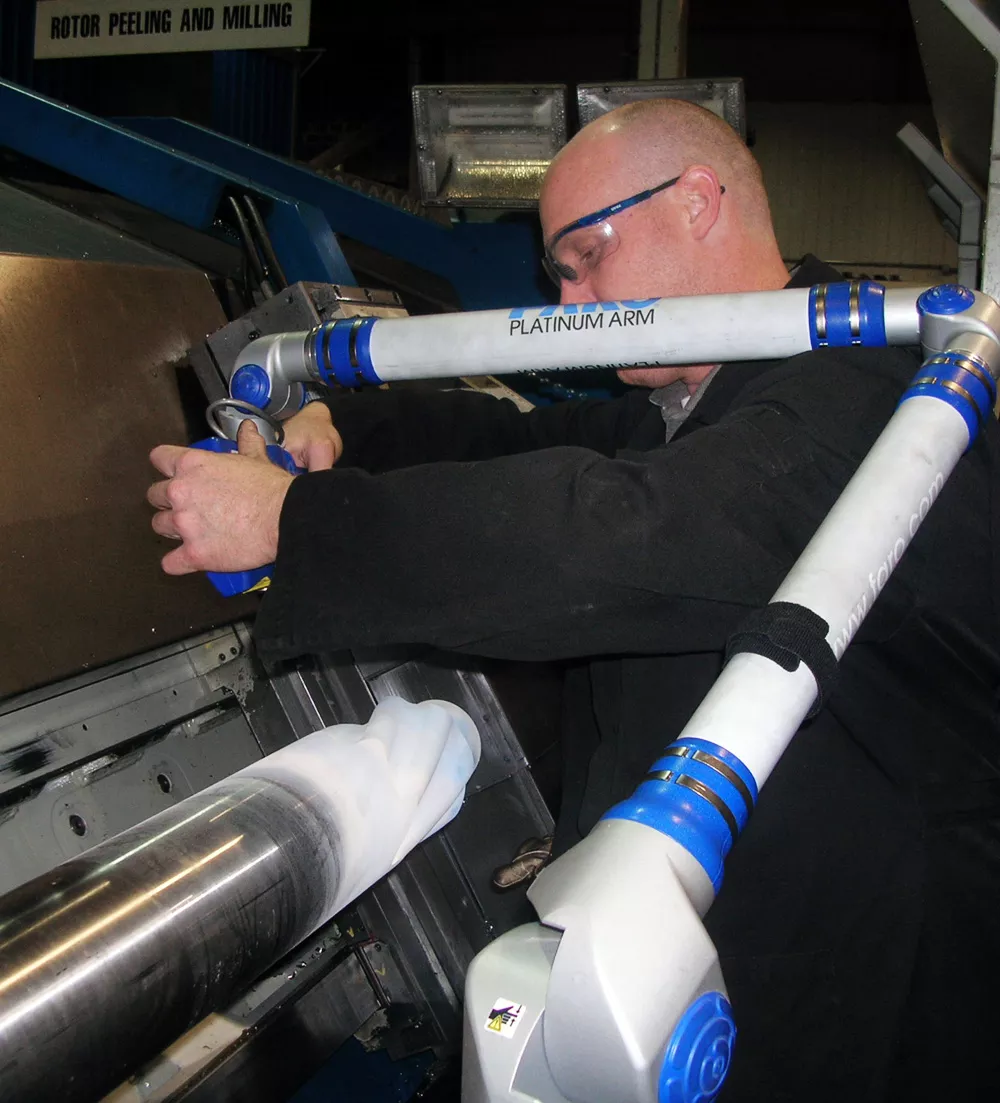
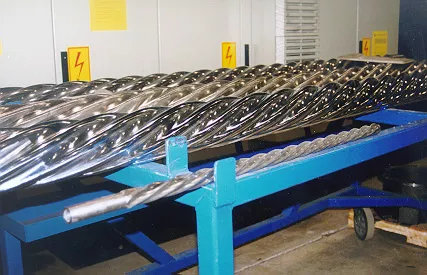
油圧セクション
以前、同社では加工後の油圧セクションの寸法検査を行うために製造部門から1人、品質管理部門から1人、エンジニアリング部門から2人の合計4人を必要とする手順を使用していました。長さが6m以上に及ぶこともあり、らせん状に曲がった大型の構成部品の検査工程では、寸法データを収集し、CADソフトウェアで作成された元の設計と手動で比較するのに約1時間かかりました。機器のオフセットは作業現場に伝達され、作業現場で加工処理に修正が加えられました。同じ構成部品の別のセクションを加工した後、このセクションにも検査プロセスを繰り返して、製品の寸法精度が修正によって向上したかどうかを確認していました。
「これは、非常に時間がかかるプロセスでした。その上、測定された製品の寸法をエンジニアリング部門がCAD図面と比較するため、それに合わせて検査作業も通常の業務時間内に限定されていました」と、Weatherford社シニアプロジェクトエンジニアのWayne Pilgrim氏は述べています。
解決策
同社は2005年に、より効率的に寸法データを収集および解析する方法を見つけるため、これらのパーツの検査工程を再評価しました。この再評価プログラムには、InnovMetric SoftwareのPolyWorks® 3D計測ソフトウェアの導入も含まれていました。寸法データを収集して設計意図と比較する作業を自動化して簡略化できる、フル機能の計測ソフトウェアです。
「オペレータの間ではPolyWorksソフトウェアの使いやすさが評判です。このソフトウェアの自動化機能はまさに群を抜いています」(Weatherford社プロダクトデザイナー、Travis Chometsky氏)。
PolyWorks|Inspector™ソフトウェアソリューションは、高精度Faro Platinumアームに搭載されるFAROレーザーラインプローブと組み合わせて使用されます。このハードウェアとソフトウェアの組み合わせにより、検査および解析時間が半分に短縮され、作業に必要な人数も4人から2人に削減できました。さらに、製造グループは検査作業に制約されることなく1日24時間シフトで作業できるようになりました。
点群データの収集
実際にFAROレーザーラインプローブでは、1秒間に最大19,200ポイントの速度で寸法データが収集されます。Weatherford社の油圧セクションの検査枠は10~15分間なので、この間に数百万の点群のデータポイントが収集されることになり、詳しくパーツ形状のデータを収集できます。
「どうしたら正確な断面を取れるかを考える数学的な部分はPolyWorksソフトウェアにお任せです」と、Pilgrim氏は述べます。「自動位置合わせ機能により、PolyWorksソフトウェアはデータ収集中のオペレータの影響を排除し、確実に一定の結果が得られるようにしてくれるのです」。
同社では、バッチベースの工程間検査方法を採用しています。「たとえば、5つのパーツを1つのバッチにまとめて製造している場合、オペレータは最初のパーツにPolyWorks/FAROレーザーラインプローブ検査プロセスを実行し、残りの4つにはPolyWorks/FAROレーザー検査なしで同じCNCプログラムを使用します」と、Pilgrim氏は説明します。「他の検査法で問題になる場合のみ、完成品を検査すればよいわけです」。
油圧セクション製品の検査工程は常に同じです。新しい油圧セクションモデルの最初の加工カット後、3Dスキャニングプロセスを通じてありのままのデータ点群が収集されます。PolyWorksソフトウェアで、この点群からメッシュが作成され、IMInspect™モジュールに読み込まれます。オペレータは、PolyWorksのデータとCADの位置合わせ技術を利用して、このメッシュをリファレンスオブジェクト (PolyWorksにインポートされたProENGINEERファイル) に位置合わせし、両方のモデルを同じ座標系で登録します。完璧に位置合わせされたら、オペレータはデータとCADとの比較を実行する必要がある断面を指定します。
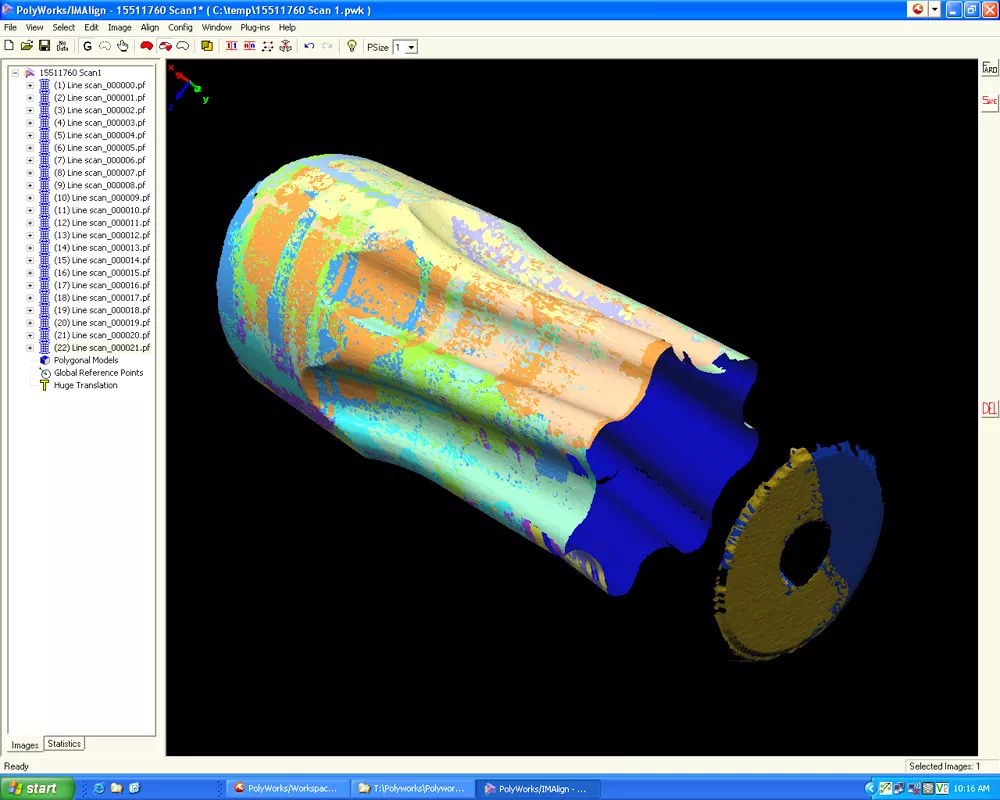
複数スキャンパスの位置合わせ
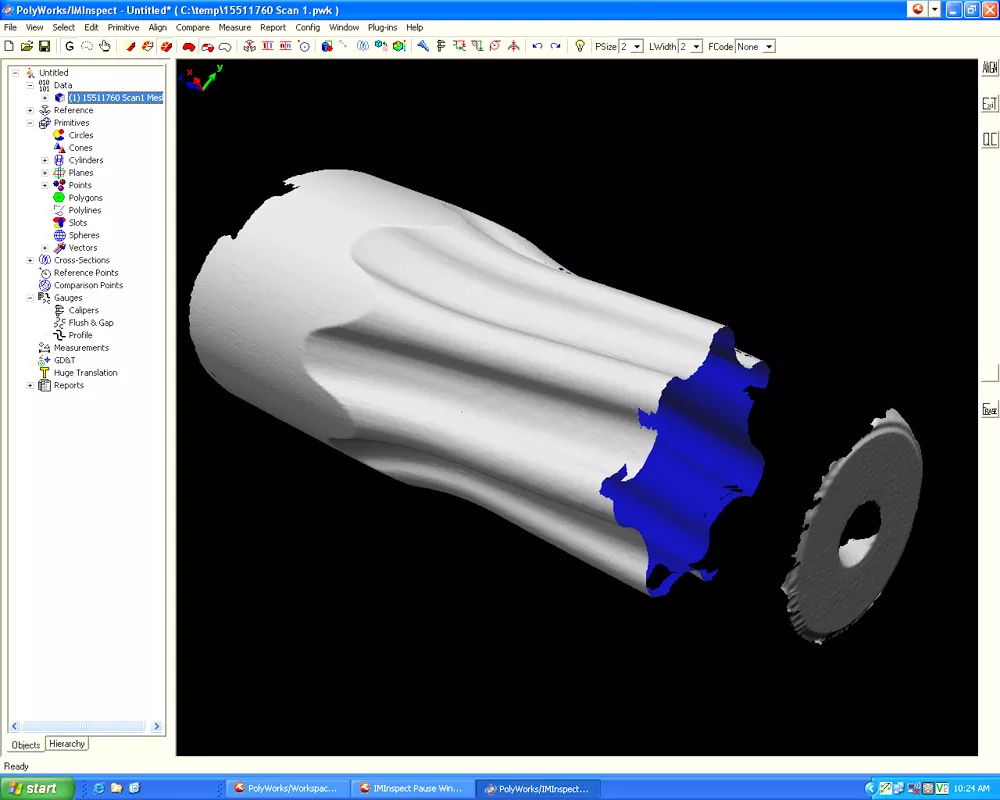
PolyWorksメッシュモデル
メリット
選択した断面ごとに、PolyWorksは自動的にデータモデルとリファレンス (CAD) モデルとを比較し、標準偏差、最大誤差、最小誤差などの一連の測定値を計算します。
また、データとCADとの比較結果を示すPDFレポートも作成され、このレポートを基に加工オペレータが調整を行います。別のセクションを加工した後、再びスキャンされ、調整が設計意図に近づいたかどうかを確認します。
「豊富なプログラミング経験がなくても、プロセスを素早く設定できます。マクロプログラミング言語は簡単で使いやすく、処理はコマンドウィンドウに記録されます。私たちは、この検査工程によって製造工程で時間と経費を節約できることを証明できたので、今後は他の部署がこの工程を実装するのをサポートしていくつもりです」と、Weatherford社プロダクトデザイナーのTravis Chometsky氏は語っています。強力なマクロプログラミング機能により、オペレータはPolyWorksで新しいパーツごとに位置合わせや比較タスクを手動で行う必要がありません。マウスを1回クリックするだけで、スキャンされるセクションごとに位置合わせから比較、レポート生成までの検査プロセス全体が自動的に実行されます。